Designing and crafting a diamond ring is an intricate process that takes time, patience and, most importantly, expertise. There are several different methods for each step of the ring crafting process and every jeweler's process evolves differently with time and new technology. Let's take a look behind the curtain to see an overview of common methods – and learn how we craft a wedding or engagement ring, from start to finish!
Designing
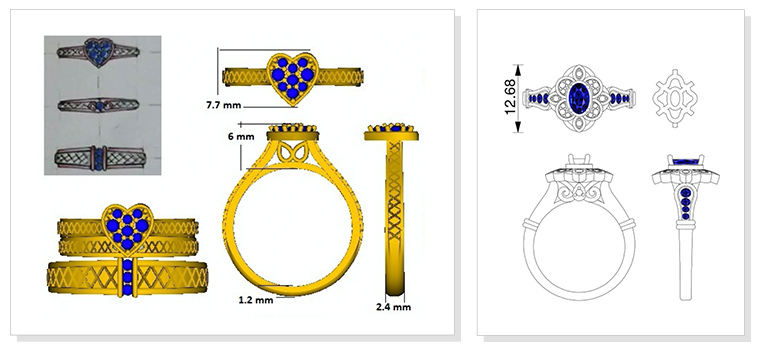
Before jewelers can craft a ring, they must have a vision or inspiration for its unique design. The first step is straightforward: taking out a pen and paper, and sketching the ring to capture its specific design features. Once an artisan is happy with a sketch of the ring, he can start to build a prototype with more high-tech tools.
Jewelers today often use CAD – computer-aided design – software to translate the rough sketch into a precise model of the new ring. This digital version can then be 3D printed in wax, the first tangible model of the ring. CAD software and 3D printing production have made it much more efficient to test and create jewelry designs prototypes. In the past, an artisan would have to hand-make a costlier silver or gold prototype, which would have to be melted down with each modification. Couples benefit from this because the new process is streamlined and replicable; they get the craftsmanship and expertise of a professional jeweler, with a faster turnaround and a more affordable price.
Molding
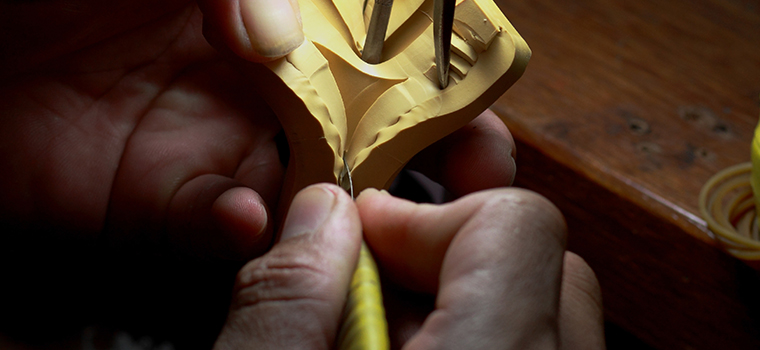
The artisan is now ready to make the mold that can be used – over and over again – to create a gold ring from the design they've envisioned. Within a mold frame, a jeweler tightly surrounds the model ring they want to replicate with pieces of rubber. They place it in a piece of equipment called a vulcanizer, which applies extreme heat and pressure to the mold frame, turning the rubber within it into a solid block – with the ring at the center. The jeweler lets the mold cool completely, then carefully slices around the edges of it with a sharp blade. The rubber mold splits into two even pieces, and the ring is freed from the center, leaving behind its exact shape in negative space. Watch a to see how a rubber mold is cut. This mold can now be injected with liquid wax to create a precise replica of the original design!
One Mold, Many Copies
Once an artisan has gone through the process of making a rubber mold for a particular design, they can use it again and again to make the same ring. But if they want to make any modifications to the design – even making the band a millimeter wider, or changing the position of the prongs – they must make a completely different rubber mold.
Injecting
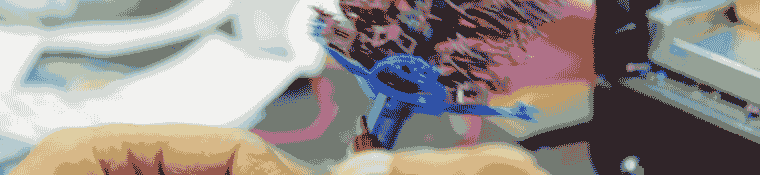
Once jewelers have made a wax replica of the ring they'd like to cast in gold, they attach it to a "wax tree," which is submerged into to a plaster bath that fills every groove of the wax model rings. Once the plaster dries and has solidified, the plaster molding is put into an oven, causing the wax to liquify and evaporate, leaving a negative space in the plaster mold.
Molten gold is poured into the plaster caste while in an oven, producing a large gold tree of wedding rings. The gold ring that comes out of the mold doesn't look much like the shiny jewelry you're used to. It is still very rough and unfinished, and it needs to be sanded and polished.
Polishing
The artisan begins the painstaking process of smoothing out the rough edges of the gold ring – filing, grinding, and polishing until the surface is perfectly smooth and shiny.
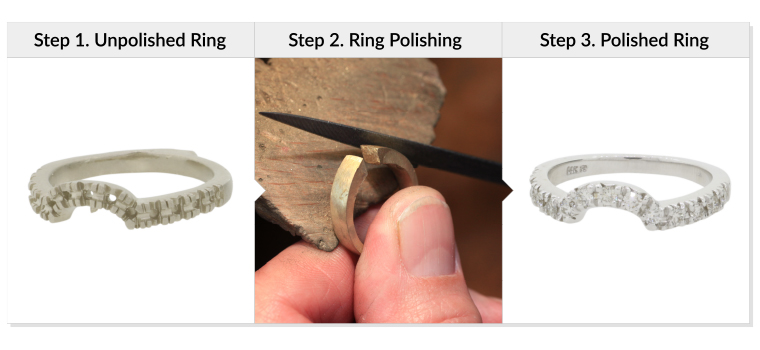
- Yellow Gold: Yellow gold reflects its natural color when the polishing process is complete, and it requires only occasional repolishing to maintain its lustrous shine.
- White gold: White gold requires a rhodium polish which is what gives white gold jewelry its lustrous shine. The piece will require more frequent repolishing or "redipping" from a jeweler to keep its color and shine over years of wear. Rhodium is applied through a process of eletroplating, the same way paint is applied to metals, such as on a car's exterior.
To learn more about gold colors and their compositions visit our gold guide!
Setting
Once the gold ring is polished to perfection, it's ready for the final (and most important) step: setting the diamonds. There are many different setting styles, but prong settings and channel settings are two of the most popular.
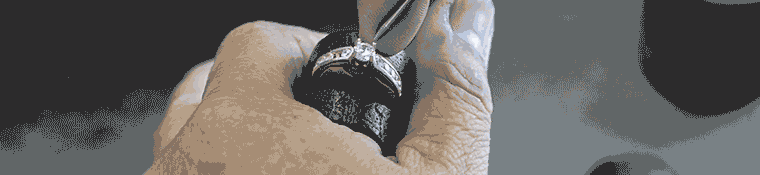
For a prong setting ring, small hook-shaped metal pieces hold diamonds firmly in place. The jeweler files all of the prongs down to the right size and rounded shape, then places each diamond individually in a gap between prongs. They then bend the prongs around the stone's girdle to secure them through a process called prong cupping.
In a channel setting ring, diamonds are suspended between two strips of metal, called channels. After the setting is completed we enter the final stage of crafting!
Quality Control
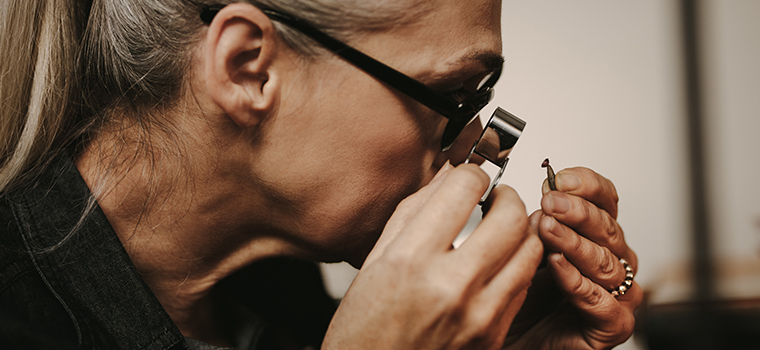
An important step in the crafting of fine jewelry, quality control of diamond and gold jewelry includes many aspects such as:
- Tap testing each stone to ensure it's securely fastened by prongs
- Sizing verification to ensure the ring is correctly sized.
- Visual inspection, to ensure symmetry as well as design characteristics were met.
The founding of My Trio Rings came from many generations of experience in the Diamond and jewelry industry. This allowed us to identify points in the crafting process which could be made more efficient and therefore a lower cost to couples seeking our wedding rings.
Over the years since our founding of My Trio Rings in 2009, we've developed quite a few advancements in the supply chain that have helped us to serve our couples better, such as improving production times to less than 14 days (half that of major brand name retailers!) and connecting the crafting floors production times to the filter on our website which lets you see what rings can be delivered in time for your wedding.
We hope you've found this overview of how our rings are crafted to be informative, if you have any questions about this process, reach out and say hello to our expert team!